Lubricant Condition Monitoring: Key to Equipment Reliability
The lubricating oil circulating around within an operating engine or machine is similar to the blood
circulating within the living human body. Just as samples of the blood can be extracted and examined in
a quest to identify the health state of the blood owner, samples of lubricating oil circulating around
within a machine can also be indicative of the health of the machine. The advantage of monitoring
lubricant is that the lubricant is highly likely to carry the evidence of faults from a variety of
positions within the machine to some point where a monitor can be fitted or from where a sample can be
drawn. Lubricant Analysis can be used for the following two purposes:
1) Monitoring the condition of a Lubricant
2) Monitoring the condition of the Equipment
Used Lubricant analysis is both proactive and predictive. The operational life of most industrial
machinery is directly related to the contamination and chemistry of the lubricants. By monitoring and
reporting contamination issues, oil analysis is possibly the most valuable proactive condition
monitoring technology available for improving equipment reliability. The following are the aims of
Condition Monitoring of Lubricants -
1) Determine Lubricant Condition / Quality
2) Identify and quantify contaminants
3) Optimize lubrication change interval
4) Verify the equipment's abnormal condition
5) Enhance the scheduling of repairs
6) Enhance troubleshooting
7) Monitor / Verify maintenance activities
8) Develop complete profile history
9) Aides in the equipment performance and replacement evaluation
Advanced Methods for Lubricant Condition Monitoring
Monitoring the condition of lubricants is essential to ensure the smooth operation and longevity of machinery. For systems with less than 250 liters of lubricant, analytical testing may not be justified, and maintenance intervals are typically determined based on experience. However, in larger systems containing over 250 liters, regular testing becomes crucial to assess when the lubricant approaches the end of its useful service life. A combination of spot testing and laboratory analysis is recommended for comprehensive monitoring.Spot Testing:
Visual Test: Examine the lubricant's clarity and color. Both foaming (air and oil mixture) and emulsions (water and oil mixture) can render the oil opaque. Foaming is often caused by mechanical factors like excessive churning or high-pressure oil return impingement. It may be stabilized by certain contaminants. If excessive foam has no apparent mechanical cause, consider changing the oil.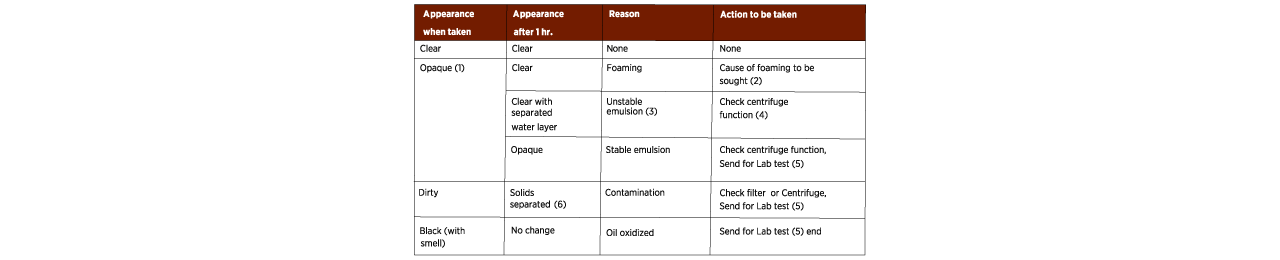
Odor Test: Oxidized or biodegraded oil tends to have an unpleasant smell, which can serve as an early indicator of lubricant degradation.
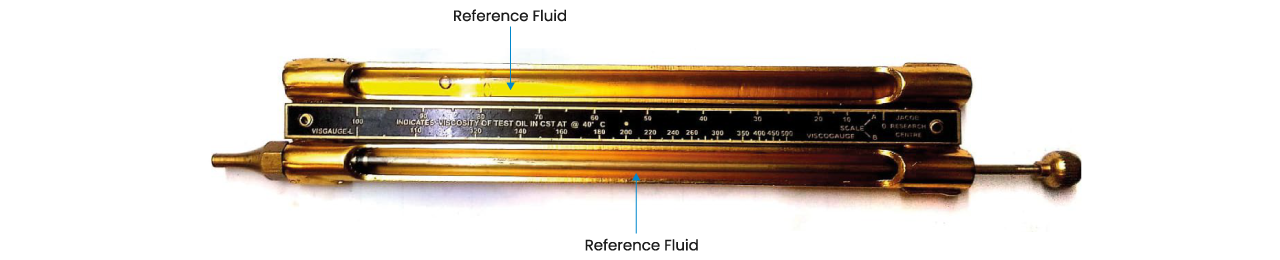
Viscosity Comparison: Compare the lubricant's viscosity with that of new oil. A significant increase (around 15%) in viscosity may indicate degradation, warranting an oil change.
Blotting Test: Use this test to check for the presence of water and dirt in the lubricant, both of which can compromise its effectiveness.
Crackle Test: The hot-plate crackle test is a simple way to detect free and emulsified water, the most problematic forms of water in oil. It involves heating a drop of oil on a hot plate and observing the number and size of bubbles as water vaporizes.
Interpreting Results: If viscosity increases by 15% due to degradation, consider changing the oil. In cases where changes are caused by contamination or topping up with the wrong oil grade, different limits may apply. Acidity levels rise due to oxidation, which accelerates over time. While these acids aren't corrosive to equipment materials, measuring acidity provides valuable insights into lubricant conditions.
Therefore, effective lubricant condition monitoring techniques are essential for maintaining machinery health. Early detection of issues through spot testing, including foaming, odor, viscosity, blotting, and crackle tests, can prevent costly breakdowns and extend equipment life. When dealing with larger systems, combining spot testing with laboratory analysis ensures a comprehensive approach to lubricant maintenance, helping industries achieve optimal performance and reliability.
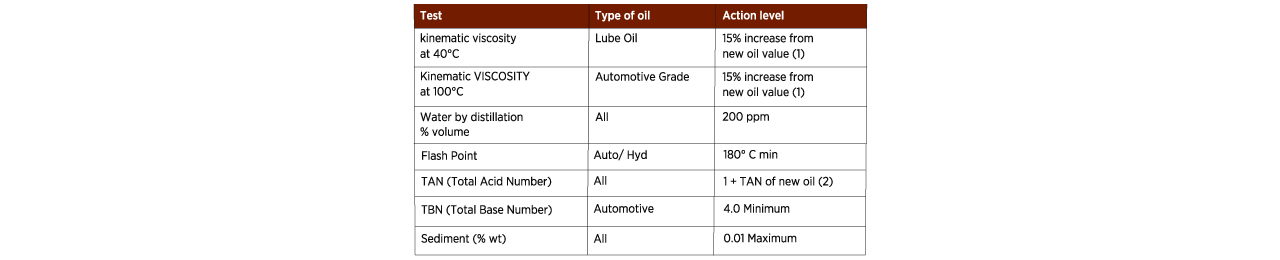
Techniques for In-Depth Equipment Health Evaluation
Monitoring equipment conditions is essential for optimizing machinery performance and preventing costly breakdowns. Three widely used techniques for this purpose are Particle Counting, Spectroscopy, and Ferrography.Particle Counting: Particle counting assesses wear particles and contaminants in lubricants, determining their concentration. ISO 4406 and NAS 1638 are two common standards for evaluating oil cleanliness levels. ISO 4406 uses cumulative counts, e.g., particles larger than 5 microns, while NAS 1638 employs differential counts, e.g., particles between 5 and 15 microns. An increase by one code level represents a doubling of particle counts. ISO 4406 distinguishes between silting (particles smaller than 5 microns) and wear catalysts (particles larger than 15 microns).
Spectrometric Elemental Analysis: Spectroscopy identifies elements (wear particles, contaminants, and additives) in lubricants and quantifies their concentrations in parts per million (ppm). Monitoring 22 elements associated with wear metals (e.g., iron, copper), lubricant contaminants (e.g., silicon, boron), and additive depletion (e.g., phosphorous, zinc) helps in assessing lubricant health. This technique is effective for small particles but may not accurately detect severe wear particles larger than 10 microns.
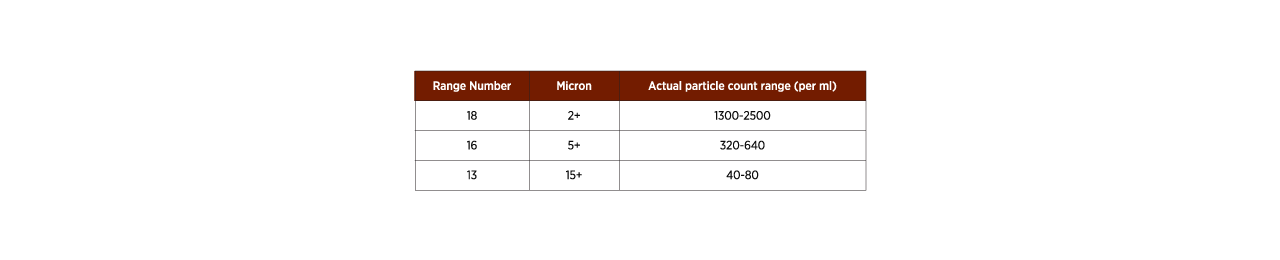
Integrating Vibration and Oil Analysis for Machine Condition Monitoring
Vibration analysis and oil analysis are pivotal techniques for assessing the health of machinery, often chosen by industries like power generation, petrochemicals, and steel. While each technique offers unique advantages, its true power is unleashed when integrated into a unified condition monitoring program.Advantages of Oil Analysis: Oil analysis stands out for providing early and direct insights into wear modes and machinery conditions. It serves as a leading indicator of active machine wear, surpassing even vibration analysis in some cases. Additionally, it excels in monitoring low-speed machinery, where vibration analysis may be challenging. However, oil analysis alone may not unveil all failure mechanisms comprehensively.
Vibration Analysis Strengths: Vibration analysis is highly effective in detecting faults in high-speed journal-bearing systems and localizing the point of failure. It complements oil analysis by pinpointing specific issues in these systems. Nevertheless, it may not always provide insights into the wear mechanisms inducing failure.
The Synergy of Both Techniques: The combination of oil analysis and vibration analysis has proven to be a winning strategy for comprehensive machine condition monitoring. These techniques often serve as leading and confirming indicators of machine failure. Oil analysis excels in gearboxes, hydraulic systems, and reciprocating equipment, while vibration analysis shines in high-speed journal-bearing systems.
Effective Root Cause Analysis: Together, they offer an enhanced ability to determine the root causes of failure. Oil analysis excels at identifying wear mechanisms, while vibration analysis aids in localizing the failure point. This combined approach helps in diagnosing and addressing machine health issues more effectively.
Correlation and Conclusion: Overall, oil analysis and vibration analysis correlate well, providing a holistic view of the machine's condition. Although there are instances of contradictory results, the synergy of these techniques is indispensable in controlling the root causes of machine failure and ensuring optimal machinery performance. In essence, integrating these two techniques is a game-changer in the realm of predictive maintenance, delivering significant benefits in terms of cost savings and enhanced reliability.
One notable example is the Palo Verde Nuclear Generating Station, which successfully combined both techniques into a unified group, resulting in remarkable cost savings of approximately $3.7 million in just one year. The fusion of oil analysis and vibration analysis is a best practice that continues to gain traction across various industries, leading to more proactive and effective machine condition monitoring.
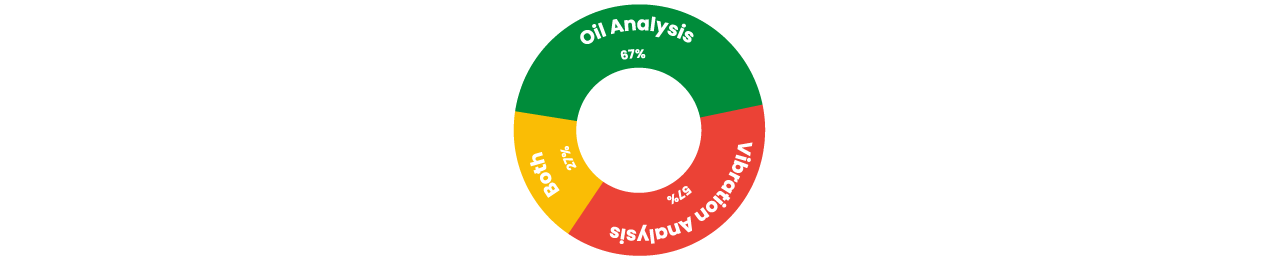
Condition Monitoring of Bearing Lubrication Condition:
Whether the bearing has sufficient lubrication or not, can be found out by two techniques:
1) Shock Pulse Measurement
2) Acoustic Emission Monitoring
1) Shock Pulse Measurement: The difference between SPM and Vibration Measurement can be illustrated by showing what happens when a falling metal ball strikes a metal bar. At the moment of impact, the colliding molecules will cause a pressure wave to spread through both bodies. The magnitude of this wave is a function of the speed of the colliding bodies. It is independent of their masses and shapes. The SPM method analyses the first stage event, the “shock pulse” traveling through the material of the bar. The impact will then cause the bar to vibrate. This vibration is a function of the speed, mass, and shape of the bodies. Vibration measurement is used to measure the movement of the bar. When hit by a shock wave, a shock pulse transducer responds at its own resonance frequency of 32 kHz. It will magnify the high-frequency shock signal, while all machine vibration is filtered out. The output of the shock pulse transducer is a rapid sequence of electric pulses, proportional to the amplitudes of the shock waves. Shock pulses are measured on a decibel scale (dBsv= decibel shock value). The absolute shock pulse level of a bearing, measured in dBsv, is both a function of rolling velocity and of bearing condition. To neutralize the effect of moving velocity on the measured value, the instrument has to be programmed with:
• Shaft diameter (in millimeters or inch)
• Rotational speed (in rpm).
The instrument will then calculate the initial value dBi, the starting point of the condition scale for a particular bearing. The instrument takes a sample count of the shock pulses occurring over a period of time and displays;
• The maximum value dBm for the relatively small number of strong shock pulses
• The carpet value dBc for the large number of weaker shock pulses.
The maximum value dBm defines the bearing’s position on the condition scale. The difference between dBm and dBc is used for a finer analysis of the causes for reduced or bad conditions. An increase in dBc with dBm within the limit shows insufficient lubrication.
2) Acoustic Emission Monitoring: Acoustic monitoring has for many years been successfully utilized to monitor the condition of electrical systems and identify leaks in vacuum, compressed air, steam, and other fluid transfer operations. In recent years, more and more maintenance professionals have come to rely on this technology to monitor the condition of mechanical components and even monitor bearing lubrication conditions. The amount of noise produced by a lubricated bearing can be a useful indicator of the effectiveness of the lubricating film. Rolling element bearings typically employ an elasto-hydrodynamic lubricating film. In this type of lubrication, the loaded surfaces elastically deform and the load is carried by a film of oil sufficiently thick to prevent the interacting surfaces from contacting one another. At a microscopic level, the finished surfaces in the bearings present irregularities or bumps often referred to as asperities. When they collide, it generates noise which can be measured by the Acoustic Monitoring Device. In a properly lubricated bearing, these collisions should be few and, thus, generate a relatively low noise level, but as the grease in a bearing is “used up”, the oil film begins to dissipate and the collisions become more frequent and create more noise. While it is certainly possible to hear this phenomenon with a stethoscope, the acoustic instruments allow it to be quantified and provide an objective interpretation of the sound levels. Based on the normal or baseline noise levels for a particular bearing, limits can be established that alert the technician to the precise time the bearing requires re-lubrication and even indicate when to stop applying grease to prevent over-lubrication. One such acoustic emission instrument is shown below. Distress readings are taken by the instrument. When bearings are found with a value >10, it is time to re-lubricate. The reduction in distress confirms the improvement. If there is no reduction in distress value after relubrication, it indicates bearing damage.
Benefits of Condition Monitoring of Lubricants:
Lubricant analysis can be a first line of defense against catastrophic equipment failure. Condition Monitoring of lubricant can detect minor changes in the lubricant before they cause damage to the equipment, detect minor wear and corrosion problems before they cause major equipment damage, and identify contaminants so corrective action may be taken to eliminate these contaminants before they cause equipment damage. There are many examples where conditions monitoring of lubricants and corrective actions have given substantial benefits to the organization. At Chiba Mill of Kawasaki Steel Company Ltd., oil contamination control in the hydraulic system resulted in a 97% reduction in hydraulic system malfunctions over a period of 5 years. The piston pump's average life increased from 12 months - 24 months. Data given below shows, how bearing life is affected by both particle and water contamination. Substantial life improvement in bearing life can be achieved by monitoring both particle and oil contamination and controlling it within the desired limit.
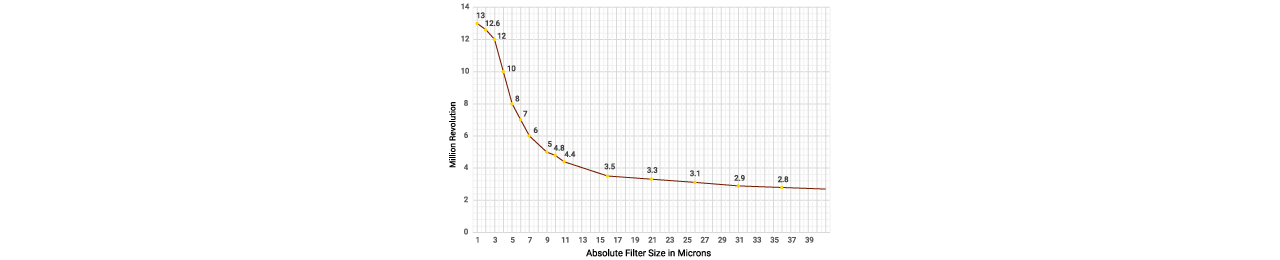
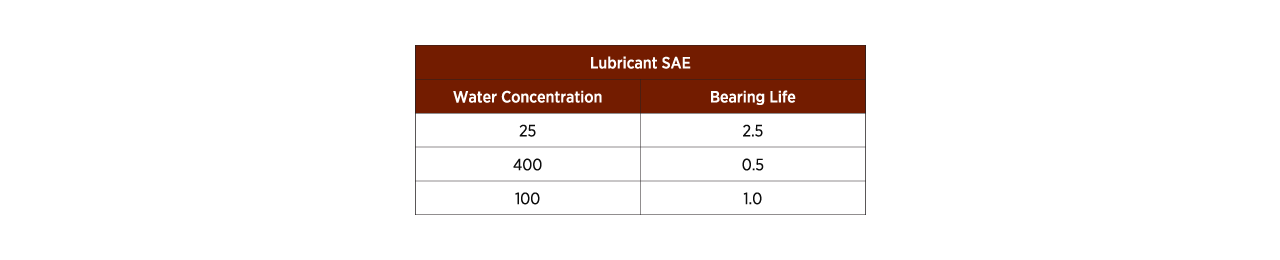
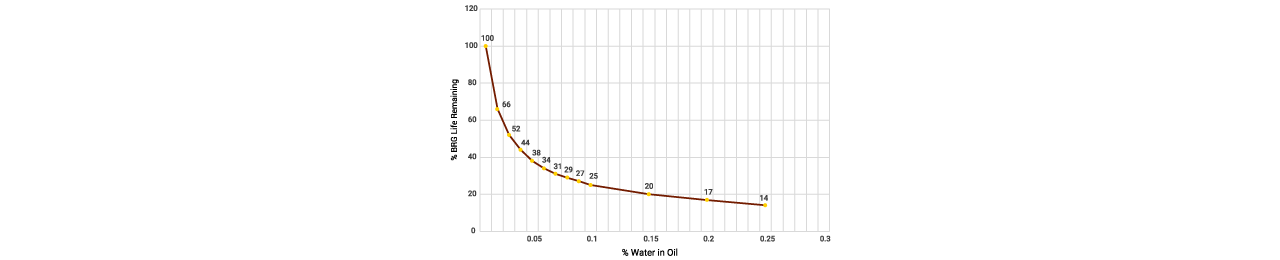

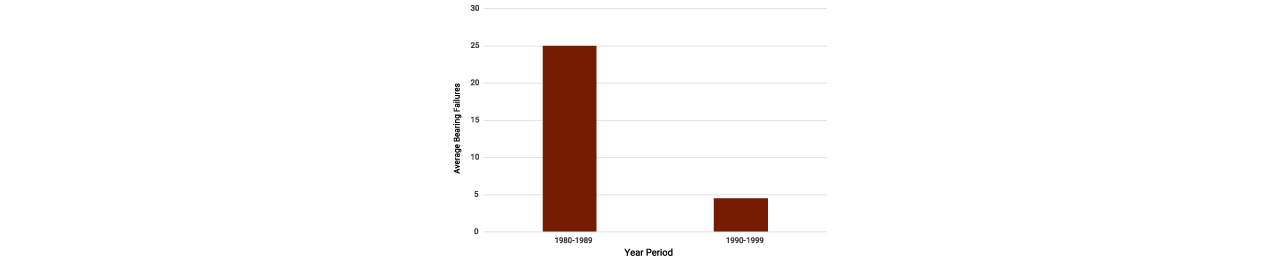
Companies have realized the importance of lubricant analysis as a means of reducing damage caused by wear or poor lubrication. Lubricant analysis helps to identify contamination, lubricant degradation, and abnormal machine wear. With the focus on enhanced asset reliability to avoid unscheduled machine downtime, condition monitoring of lubricants is growing to be an increasingly important aspect of every organization’s predictive maintenance program.
About the Author
Mr. G.R.P. Singh with 34 years of steel plant maintenance expertise and a BE Mechanical Gold
Medalist
from BIT, Mesra, is deeply passionate about hydraulics, plant equipment condition monitoring, and
root cause failure analysis. He actively contributes to his field by serving as the Secretary of the
Condition Monitoring Society of India, Jamshedpur Chapter. He holds memberships in the Tribology
Society of India and the Institution of Engineers. Currently, he plays a pivotal role at Tata Steel.
Contact Mr. G.R.P. Singh at grpsin@tatasteel.com
G.R.P. Singh
Head of the Quality Assurance Group | Tata Steel Ltd.