Sustainable Solutions for Rolling Mills Bearing Lubrication - A Holistic Approach
In metalworking, rolling is a metal forming process in which metal stock is passed through one or more
pairs of rolls to reduce and
uniform the thickness. Rolling is classified according to the temperature of the metal rolled. The
process is called hot rolling if the
temperature of the metal is above its recrystallization temperature. In the case of cold rolling, the
temperature of the metal is below
its recrystallization temperature.
Working Condition Environment of Rolling Mill Bearing Lubrication
Basically, rolling mill bearings are exposed to high temperatures, load, speed, water wash-outs, dust,
and contamination.
It is observed that the mill parameters and the variables wherein we observed the same viscosity grease
in the application for high speed,
lesser speed, and load.
Secondly, regarding lubrication top-up, it is observed in fixed intervals, The bearing failure was
observed because of rise in temperature.
The temperature rise was because of excess Lubrication also frequent Re-lubrication intervals were
observed.
Why Calcium Sulphonate Complex?
Calcium Sulphonate Complex is suggested to the customer for the following benefits:
- Compatibility with existing grease
- Higher drop point
- Better load-bearing capacity
- Water wash-outs
- For effective lubrication and as per the speed factor high speed, for roller bearing lubrication, it is recommended lesser viscosity grease helps in achieving extended re-lubrication intervals
- Better housekeeping - the application criticality is observed and high-speed roller bearing lubrication as per standard DN factor worked out and lesser viscosity lubricant was suggested for the high-speed bearings
A case: our experience
Our customers were into rolling Mill 500 TPD and manufacturers of TMT Rebars & Wire rods. We helped them
reduce the number of bearing failures
with extended lubricant hours and minimize the total cost of ownership.
Consumption Calculation for bearing No. 24030 -
=(0.005*150*76)
= 57 Grams
We studied the application in detail and offered a solution Calcium Sulfonate Complex, which took care
of the load, high temperature,
and good water washout. The technical superiority offered through the products was:
- Better drop point
- Load carrying
- Temperature resistance
- Excellent water washout
Results: Re-Lubrication extended from 8 hrs to 20 hrs and Bearing failure was not observed over the last 4 months, savings in man hours. Because of extended re-lubrication intervals less fatigue to the operation team. Our experience shows that in general for this application the clients use EP 2 Type Grease. Despite having no problems in regular runs, our clients would admit that in times of great production and heat, they are accustomed to incidents with frequent relubrication and bearing failures. Bearing failures and change-over add to the cost of lost production hours and expenditures on maintenance and bearing costs.
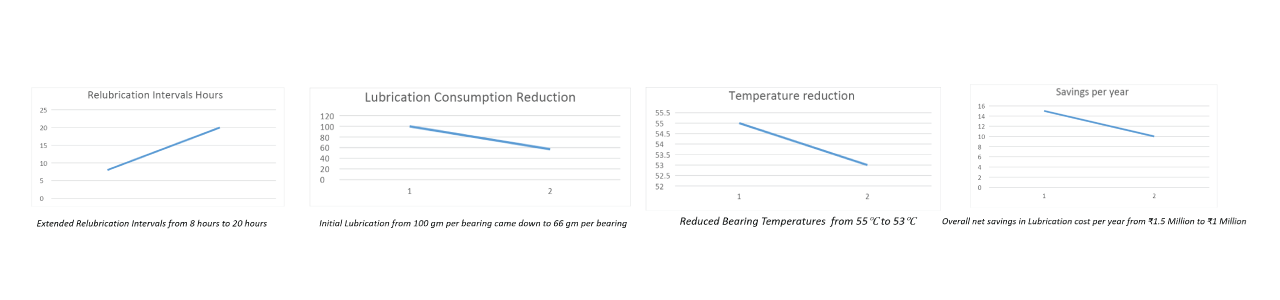
- Less Co2 emissions
- Lesser use of base oil, additives, and thickeners
- Less transportation and which ultimately results in less Co2 emission
- Less lubricant consumption through judicious and scientific usage
- Lesser contamination and waste handling