Oil Analysis Contribution to Effective Machine Risk Management
Across all industries, ensuring equipment reliability is paramount to achieving the company’s financial
objectives and managing potential risks associated with safety hazards, environmental impact, and
equipment failure.
Machine breakdowns not only result in significant financial losses and operational disturbances but also
contribute to increased maintenance costs and compromised safety.
A proactive approach to effectively control and mitigate risks associated with equipment involves
Machinery Lubrication and Oil Analysis Strategies.
This article does not intend to provide an exhaustive risk assessment or identify potential hazards.
Instead, the focus is on exploring how oil analysis can be a very useful tool within an effective risk
management strategy for mechanical physical assets, aiming to minimize the probability of equipment
failure and associated risks and ultimately enhancing reliability and longevity.
Reciprocal influence between lubricant condition and machine health
Whether engaged in root cause analysis studies, interpreting oil analysis results, conducting a GEMBA,
or just when thinking about important roles lubricants play inside equipment, we recognize that there is
a mutual influence between the equipment and the lubricant it relies upon. The degradation of one
affects the deterioration of the other, and vice versa.
Simultaneously, the operations and environmental conditions of the equipment significantly influence the
health of both the lubricant and the equipment.
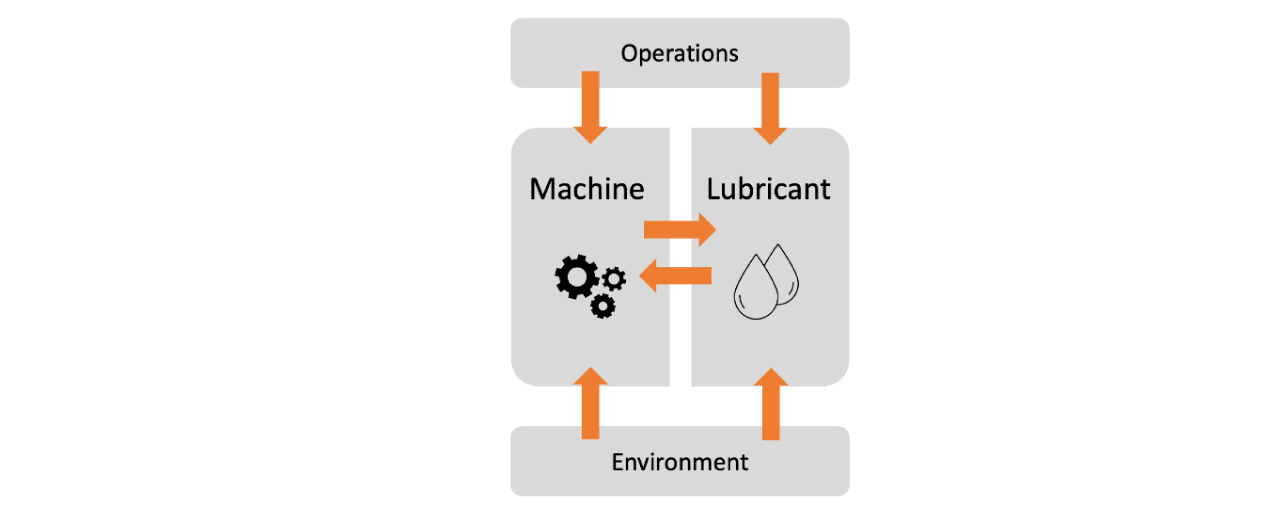
As an illustrative example of this mutual influence, let’s consider a heavy-duty diesel engine, commonly found in transportation, construction, or diverse industrial equipment.
These engines operate under extreme conditions where they undergo heavy loads and high temperatures and are exposed to diverse contaminants. Consequently, the health of the engine has a profound impact on the lubricating oil circulating within it.
During operation, these diesel engines generate significant heat. Elevated temperatures can lead to thermal degradation of the lubricating oil or its oxidation in the presence of air, water, and some other catalysts. These degradation mechanisms compromise the oil's ability to provide effective lubrication, leading to increased friction and wear within the engine components.
Another factor influencing lubricant health in such diesel engines is fuel dilution. Incomplete combustion can effectively introduce unburned fuel into the oil, diluting its viscosity and reducing its ability to prevent metal-to-metal contact, leading to increased wear, and as a result, the overall performance and reliability of the engine is compromised.
In this context of mutual influence between the equipment and its lubricant, this at last becomes a reflection of the operational and environmental challenges encountered by the equipment it lubricates. Exactly like blood is considered an information vector about human body health.
Consequently, considering the dynamic interplay between operations, environment, lubricant, and machine, becomes essential not only for ensuring the efficiency of industrial systems but also for effectively managing and mitigating risks associated with equipment.
Lubricant & Equipment Condition Monitoring
The curve in Fig. 2 below is known as the P-F curve, where:
-
‘P’ stands for the Potential Failure when a failure first becomes detectable.
-
‘F’ for Functional Failure when the equipment no longer performs its intended function.
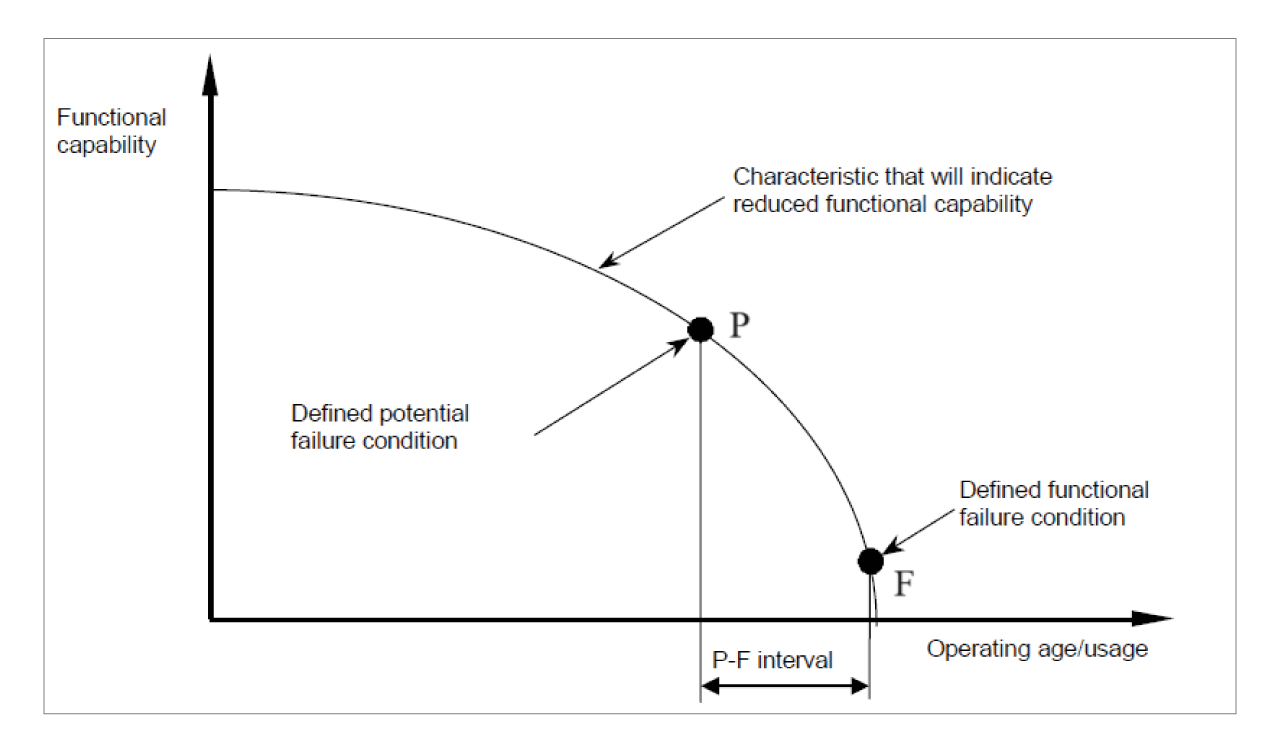
The interval for the condition monitoring task should be less than or equal to the P-F interval. The relationship between the task and P-F interval varies depending on the probability of non-detection the organization is willing to accept and the severity of the failure mode consequences. A task interval equal to half of the P-F interval is typically used, as this potentially provides two chances for the degradation to be detected [1].
Oil analysis is a condition monitoring technique that involves the systematic examination of a representative lubricant sample drawn from the equipment. This examination can be performed online through sensors, onsite by the company’s own resources, or offsite by a commercial laboratory.
This technique provides valuable insights into the condition of the lubricant and equipment, in the context of mutual influence as explained above. These insights include:
- Assessment of the properties of the lubricant (Physical, Chemical, and Performance).
- Assessment of equipment degradation.
- Assessment of contamination and the impact of operations and environment on both lubricant and machine.
Importance of Precision Lubrication
Generally, within the curve above, we pay more attention to P (Potential Failure) and the region beyond it. But at this point, the failure is already there, and its detection could be started by using the appropriate condition monitoring technique that is more suitable for its development stage. All we can do at this moment is to think about how to mitigate its consequences. However, the most reasonable and imperative question in this context revolves around what measures can we deploy to prevent a potential failure or, at the very least delay it; as much as possible.
Addressing this logical question involves thinking about what to deploy to ensure the smooth operations of a physical asset in fulfilling its intended function. Actions aimed at achieving this objective fall within the interval before P. The primary focus should be directed towards such actions, as this is the phase where failures can effectively be prevented. Regrettably, these crucial actions are often overlooked and do not receive the attention they deserve, despite their potential to offer the most favorable return on investment.
As companies mature, their focus on the region prior to ‘P’ increases. One valuable action is ensuring lubrication compliance. This is about the selection of the right lubricant, with the right quantity in the right location on the equipment and the right re-lubrication frequency, without forgetting a well-trained maintenance workforce to execute lubrication tasks following the right application methods.
Lubricants are crucial for sustaining optimal performance and ensuring the smooth operation of equipment. Their contribution is substantial across various vital aspects. Beyond merely reducing friction and preventing wear, they also contribute to heat dissipation, corrosion prevention, and acting as a protective barrier against contaminants.
The significance of Precision Lubrication is paramount right from the outset. But we should not forget that even the most reliable designs might be susceptible to factors leading to failure, necessitating therefore deploying CBM techniques from the outset. Oil Analysis can be employed both proactively, before the onset of failure, and predictively, during the development of failure.
Oil Analysis Before Failure Onset: A Proactive Condition Monitoring Technique
Proactive maintenance, by definition, involves continuous monitoring and controlling of machine failure root causes [2].
In the proactive interval on the curve above, before the potential failure, oil analysis through condition and contamination assessment helps prevent the onset of the root causes of machine failure. Common proactive oil analysis tests include:
-
Viscosity is a critical property of lubricating oil, and it is very normal to find this parameter on the
top
of all analysis slates for all kinds of equipment. Any deviation from the expected viscosity can
indicate
issues such as the usage of the wrong lubricant, top-up or mixture with the wrong lubricant,
contaminants
ingress, fuel dilution, or thermal degradation.
-
Elemental Analysis by ICP (Inductively Coupled Plasma) or RDE (Rotative Disc Electrode) informs about
additives degradation by comparing the element concentration measured in PPM to the baseline set when a
fresh sample is being analyzed. Additionally, this test can reveal the presence of undesirable elements
like
contaminants and wear metals.
-
Infra-Red Spectroscopy which covers the use of FT-IR in monitoring additive depletion, contaminant
buildup,
and base stock degradation in machinery lubricants, hydraulic fluids, and other fluids used in regular
machinery operation. Contaminants monitored include water, soot, ethylene glycol, fuels, and incorrect
oil.
Base stocks’ oxidation, nitration, and sulfonation are monitored as evidence of degradation [3].
-
Dryness Assessment involves monitoring the water content in oils, and it stands as a fundamental
component
of oil analysis programs. This primary test not only serves as an early warning system but also plays a
pivotal role in preventing failures caused by moisture-induced issues such as corrosion, viscosity
alterations, and degradation of lubricating capacity.
-
Cleanliness Assessment through Particle Count analysis is another fundamental component of an oil
analysis
slate. This test involves assessing particles by their number and size distribution. These particles can
originate from various sources, including wear debris, dust, and external other contaminant types. These
contaminants present, if left unaddressed, have the potential to accelerate wear and contribute to
premature
failure.
In the predictive interval, the maintenance team is only managing the potential failure (P) as it progresses toward the functional failures (F). At this stage, nothing will prevent the failure from happening. Lubricant degradation has already taken place to some extent, marking the initiation of equipment failure.
Oil analysis through wear debris analysis aims at examining the size, shape, metallurgy, and/or concentration of wear particles in the oil to monitor the condition of equipment components. Analyzing changes in particle characteristics over time can help identify specific components undergoing abnormal wear, enabling targeted replacement or repair to prevent catastrophic failure.
Elemental Analysis stands as a fundamental test within most of all routine oil analysis test slates across diverse applications. This powerful technique is used for wear detection at early stages as it can identify and quantify metals at low concentrations measured in parts per million (PPM). It is crucial, however, to recognize its limitations. Accurate detection is fulfilled for elements that are below five to seven microns in size. Consequently, to extend the detection range of wear particles, complementary tests like PQ and DRF, briefly introduced below, should be employed.
Particle Quantification Index (PQI), also known as Wear Particle Index (WPI), serves as the most widespread and cost-effective method for evaluating ferrous density. This test directly measures the magnetic mass of ferrous debris in the oil sample, regardless of particle size and shape. It provides a non-dimensional value that signifies the total amount of ferrous debris present in the sample. PQI emerges as a powerful tool for wear detection, particularly for monitoring ferrous particles beyond the detection range of elemental analysis. Consequently, PQI proves to be a valuable complementary test alongside elemental analysis.
Direct Read Ferrography (DRF) is another cost-effective technique to measure the wear concentrations of larger-sized particles. By leveraging the magnetic susceptibility of particles, DRF enables the calculation of the Wear Severity Index by directly reading both large and small particles. As a result, DRF stands as a viable alternative to PQI.
Analytical Ferrography is a qualitative technique that proves beneficial to understand the underlying cause or wear mode when elevated wear metals concentrations are indicated by elemental analysis, PQI, or DRF. Within this test wear particles, appearance is inspected by a microscope. This includes analyzing factors such as color, size, and shape to identify various wear modes and potential sources of wear debris.
Oil Analysis Challenges In The Context Of Machine Risk Management
The oil analysis technique brings many benefits in the context of machine risk management. These benefits include the early detection of failures by understanding the condition of the lubricating oil and the machine components, enabling timely efficient intervention before a catastrophic failure occurs. This will of course lead to reducing downtime and maintenance costs and in the middle and long term to increasing overall equipment effectiveness and reliability and extending the lifespan.
Additionally, reliability improvements resulting from effective oil analysis contribute to a safer working environment by minimizing the risk of unexpected equipment failures that could lead to accidents.
On the other hand, despite it being a powerful tool in the context of equipment reliability and risk management, its effectiveness relies on proper implementation and interpretation. Successful oil analysis program faces many challenges which may include drawing representative samples, establishing appropriate sampling intervals, establishing baseline data, combining onsite testing with offsite lab testing, ensuring accuracy of results interpretation, and combining oil analysis results with other CBM techniques like vibration analysis.
References
BS EN 60300-3-11:2009, Dependability Management. Application Guide. Reliability Centered Maintenance.
Oil Analysis Basics, Second Edition, 2010, Jim Fitch and Drew Troyer. P17.
ASTM E2412-23, Standard Practice for Condition Monitoring of In-Service Lubricants by Trend Analysis Using Fourier Transform Infrared (FT-IR) Spectrometry.