Enabling Net Zero Industrial Targets through Decarbonizing Lubricant Life-Cycle
As the world races towards achieving Net Zero emissions, industries play a crucial role in transitioning
to sustainable practices. India has already declared its goal to achieve Net Zero by 2070. Niti Aayog,
the policy maker of the GoI in its recent notification/memo No. M-11039(18)/1/2021 has formed 11
committees for implementing Circular Economy concepts in 11 focus areas. One of these is for
“Circular
Economy in Used/Hazardous Oil Wastage”. By decarbonizing the lubricant life-cycle, industries
can make
substantial progress towards their net-zero targets. With this article, let’s explore and understand the
various strategies and technologies that can be implemented to achieve this goal.
Hazardous Waste Management Hierarchy
(Taken from HAZARDOUS WASTE MANAGEMENT RULES-2016 of CPCB and NPC, MoEF, GoI)
Whenever Hazardous Waste Management is cited, the first reaction is Recycle and Recover. However, the
preventive concept of HW Management is aimed at minimizing waste generation at source by all possible
means
- Improvement in process technology & equipment which may completely eliminate waste streams;
- Improvement in plant operations; and
- Promoting prolonged use of materials through recovery/recycle/reuse of waste.
Following are the recommended steps in decreasing order of priority for HW Management.
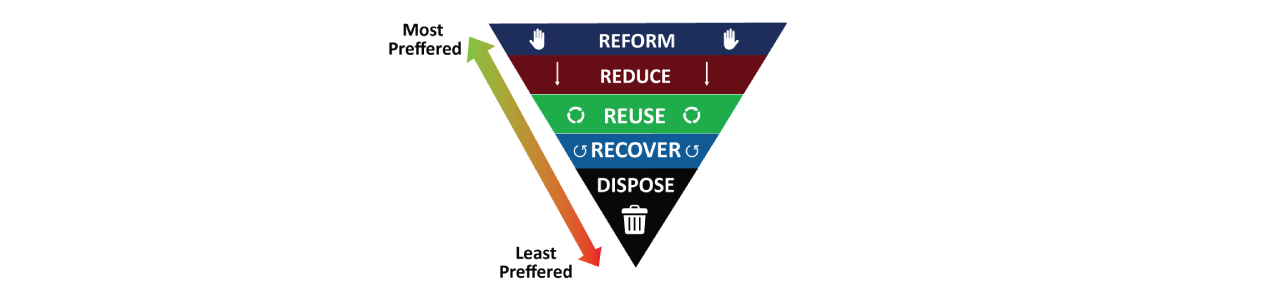
Used Oil (Lubricant) Hazardous Waste
Lubricants to rotary and hydraulic equipment with other plant machinery are analogous to what blood is to the human body. The criticality of lubricants properties directly impacts operational efficiency, reliability, and un-halted functioning of the lubricated machinery. Generation of Used Oil Lubricant is due to following reasons
- Periodic Replacement of Lubricant fully or partially as part of capital overhauls / turnarounds.;
- Leakages from equipment
- Unplanned shutdowns / breakdowns
Lubricants of various grades collected in common non-segregated tanks lead to generation of Used Oil Waste. Generally the waste thus generated is
- Disposed
- Incinerated
- Sold off to waste collection companies with no traceability of end-use.
All the above practices are considered to be of Linear Form and lead to high risk of uncontrolled GHG Emission into the environment and being paradox to the corporate ESG goals.
From Linear to Circular Economy: Understanding the Carbon Footprint of Lubricants in order to decarbonize the lubricant life-cycle, it is essential to first understand a few terms – Cradle to gate, Cradle to grave, Nano, Micro & Macro circularity.
Cradle to Gate: It refers to manufacturing and distribution of the lubricant. Oil is ready to reach the customer’s gate through barrels or tanks. This happens through direct or indirect channels of the lubricant manufacturers.
Cradle to Grave: It refers to the entire life-cycle of lubricants, from their manufacturing to their disposal. It surrounds the extraction of raw materials, manufacturing, distribution, usage, and end-of-life management. By adopting this approach, companies can minimize their environmental footprint and promote a circular economy rather than a linear economy.
Nano Circularity: This term refers to Mid-life Treatment of Oil through Oil Reconditioning Solutions. Enhancing the life of in-service lubricant right from its first fill till the end of oil’s life. This leads to reduction in new oil purchases, increasing the drain interval, lesser part failures like valves, better machinery reliability, and increase in productivity. With every 1% increase in energy efficiency there is a reduction of 2.5% of GHG emissions. Let’s not imagine the amount of resources spent on critical applications like Turbine or EH Control System due to poor lubrication management. This concept promotes “REFORM” & “REDUCE”.
Micro Circularity: This represents the End-life Treatment of Oil through Used Oil Reconditioning Solutions. When the in-service lubricant is nearing its life cycle, the oils must be collected & segregated in used oil storage tanks as per its grade. The used oil after reclamation is fit for reuse in the lubricated machineries maintaining its oil properties. The lubricant’s new-like state can be obtained by Reconditioning which is fit for use in the lubricated machinery. 100% of the used oil no longer converts into hazardous waste. This advancement is the future of lubrication. This concept promotes “REUSE”
Macro Circularity: This represents Waste Oil Collection and Recycling. Out of a billion gallons of used lubricant, only 15% approximately is re-refined. The remaining 85% is either improperly disposed of or is burnt further. The last milestone in decarbonizing the lubricant sector is through unadulterated waste oil collection and management. The re-refiners then recycle the waste oil and produce RRBO (Re-Refined Based Oil) which acts as a feedstock to the lubricant manufacturers. This concept promotes “RECYCLE”.
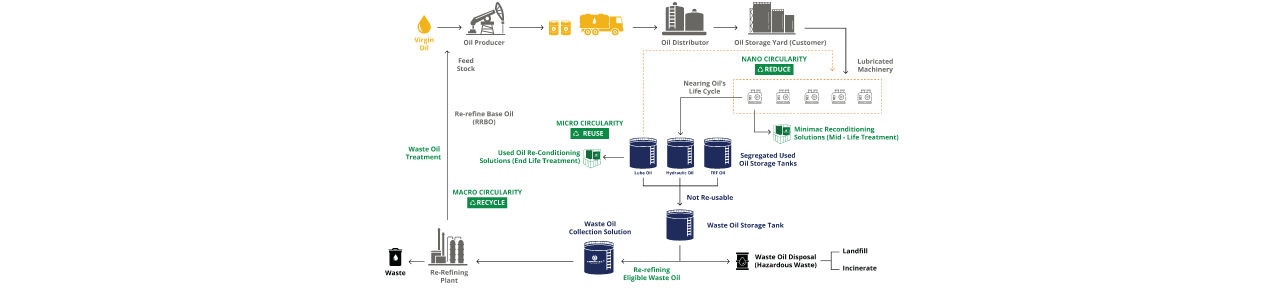
Adopting a circular economy approach with Nano, Micro and Macro Circularity through Oil Reconditioning Solutions at every stage from Cradle to Grave is the way ahead. Let’s stress upon sourcing, logistics, optimum utilization & disposal.
-
Sustainable Sourcing & Production, the first step is to implement a sustainable procedure to
source
raw materials, and do production. To support this statement, here are a few points:
- Transitioning to Renewable Feedstock: Traditionally, lubricants are typically derived from
fossil
fuels, but by shifting towards RRBOs, industries can significantly reduce their carbon
footprint.
Also, the current lubricant production ratio is 2:1, it should be certainly changed to 1:1.
- Energy-Efficient Production Process: By implementing energy-efficient and IIoT enabled
technologies
and processes in lube oil production – minimizing carbon emission.
- Optimizing Lubricant Usage: behavior needs to change; we should be responsible to use
lubricants
efficiently. A few strategies are mentioned below:
-
Effective Total Lube Management: By implementing proper lubrication management techniques and
practices – we can maximize the efficiency and lifespan of lubricants as well as machineries
thus
achieving Asset Reliability.
- Mid-Life Oil Treatment: By enabling Mid-Life Oil Treatment, the oil in use is regularly
monitored,
tested, and reconditioned for better usage and to achieve the desired lifespan of oil. This also
helps to maintain the good health of the machines and increases uptime.
- Training and Education: Proper training and education about correct usage and maintenance of
lubricants must be given to the team handling – this will lead to better practices and reduction
in
wastage and GHG emission.
- Sustainable distribution and supply chain also plays a crucial role in decarbonizing
lubricant
life-cycle. A few major focus areas are:
- Efficient Logistics: By optimizing and figuring out the best route for the distribution of
lubricant
along with sustainable packaging will help reduce carbon emissions associated with the
distribution
process.
- Adoption of Renewable Energy: With the help of companies and suppliers, the transition from
petroleum
vehicles to renewable energy-sourced vehicles can be done; thus, reducing a lot of carbon
footprint
while transportation.
- End-Life Management & proper recycling management of lubricant oil is vital to achieving
net-zero
goals.
A few important points are mentioned below:
- Organized Used Oil Collection Centers: Pilferage proof solutions should be made available easily
and
economically in front of the customers. Organize the unorganized sector.
- Recycling & Reprocessing: Technological advancements and re-refining plants must be set up to
produce
better quality of RRBO (Re-refined Base Oil) which is cost efficient and better in quality.
- Proper disposal: The waste lubricant which is not fit for recycling must be disposed of through
re-refiners or organized channels using technology.
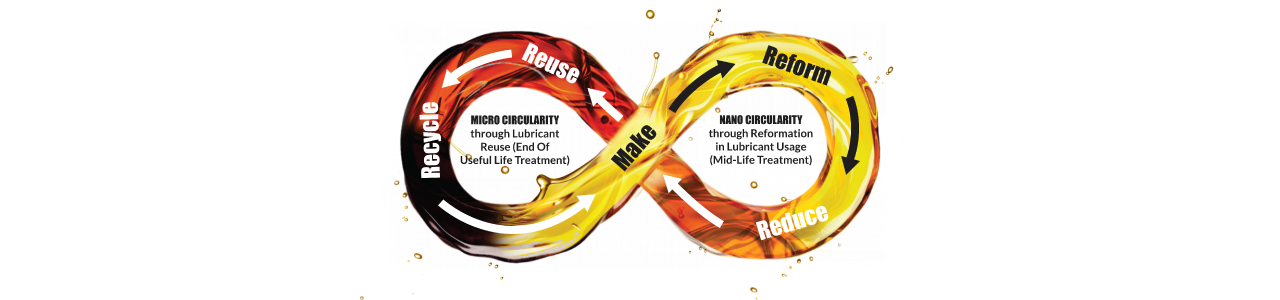
In order to reach the net-zero industrial aim, a thorough strategy that takes into account the entire lubricant life-cycle is needed. To contribute to a sustainable future, all stakeholders should work together to decarbonize the production, usage, distribution, and end-of-life management of lubricants. The technologies and tactics discussed in this article will undoubtedly lay out a clear path for the sector to follow as it strives to adopt more eco-friendly practices and solutions and move towards a net-zero carbon future. Please Note: The terms used in this article are coined by the Minimac Team and thus cannot be copied or used anywhere else.